Strategic initiatives transform DC’s performance and safety
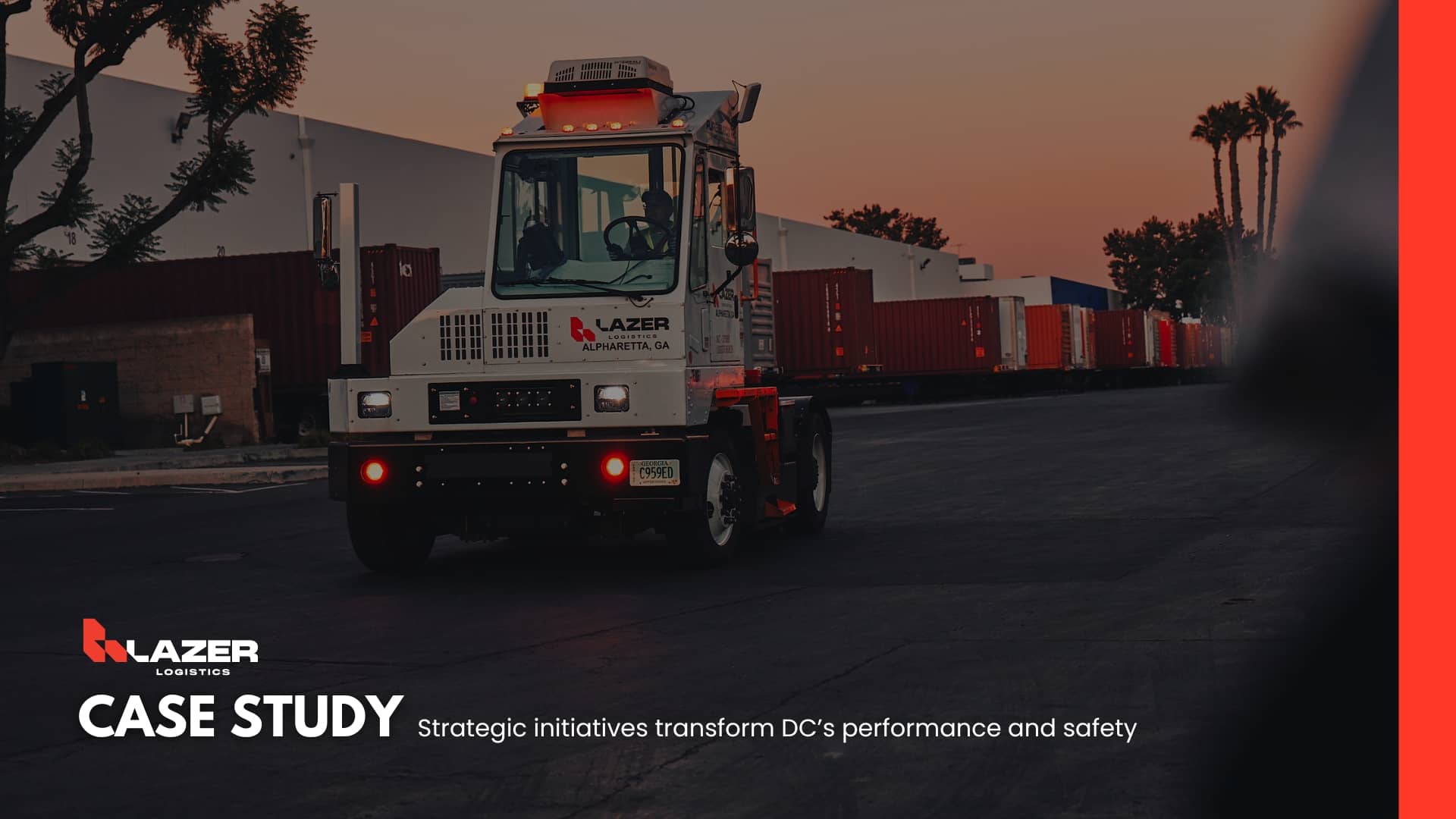
Backstory
Lazer Logistics faced multiple challenges when it acquired a distribution center for a discount retailer. The operation experienced high claim costs, an increased number of accidents and near misses, high driver turnover, and significant variance in wait times for yard spotting moves. In response, Lazer conducted a diagnostic analysis to identify the root causes and collaborated with the customer to develop an improvement plan. This case study explores how Lazer’s strategic initiatives improved safety, efficiency, and transformed overall performance at the distribution center.
Diagnosis
Lazer identified several critical issues that contributed to the distribution center’s challenges during the diagnostic analysis. The site had limited safety procedures, such as outside external lighting to indicate trailer safety and a physical bumper. Additionally, too few yard-spotting trucks and drivers resulted in a high workload for the existing drivers, increased accident rates, and driver attrition. Furthermore, several nearby facilities offered higher wages for similar positions, exacerbating Lazer’s driver retention problem.
Proposed Solutions
Lazer and the customer collaborated to develop a comprehensive plan to address the identified issues and enhance the performance of the distribution center. The proposed solutions included:
Increasing the Fleet
Lazer recommended adding one truck to each shift. This measure aimed to reduce wait times and ensure a sustainable pace of 5-6 moves per hour, mitigating driver fatigue and decreasing accident rates.
Adding Locks
Lazer introduced physical locks on trailers, which were only removed when the trailers were empty. This measure eliminated the risk of near-misses and accidents caused by spotters attempting to move trailers with personnel inside.
Enhancing Wages
Lazer proposed offering wages 11% above the local market rates to attract and retain qualified drivers. By providing a competitive compensation package, Lazer aimed to reduce driver turnover and improve driver satisfaction.
Key Takeaway
Employing an experienced lead driver: Lazer deployed one of its best drivers as a lead driver at the site. This experienced professional was a role model, guiding the other drivers while maintaining high-performance standards.
Outcomes
Implementing the improvement plan yielded significant positive outcomes for the distribution center. The following results were achieved:
Accident Costs
Direct and indirect costs related to accidents fell by 57%, surpassing the cost of adding a spotter truck. Implementing safety measures and the reduced workload per driver contributed to this substantial reduction.
Spotting Turnaround
The wait times for yard spotting moves dropped to just 5 minutes, 83% lower than the customer’s target. This improvement significantly increased the overall output and efficiency of the facility.
Enhanced Safety
Physical locks on trailers eliminated all near-misses involving spotters attempting to move trailers with personnel inside. This measure drastically improved safety conditions at the site, reducing the risk of accidents and injuries.
Driver Retention
Previously experiencing an average turnover rate of 115% per year, the Lazer achieved driver stability for 24 months. The combination of increased wages, an additional driver and truck, and a supportive lead driver created an attractive work environment for the drivers.
Conclusion
Overall, the initiatives implemented by Lazer resulted in an estimated annualized value of $250-300K for the customer, derived from the cost savings associated with reduced accidents, improved efficiency, and enhanced driver retention.
Lazer Logistics’ strategic initiatives successfully transformed the performance and safety standards of the acquired distribution center. By addressing the root causes of the operation’s challenges, Lazer improved safety procedures, increased fleet capacity, enhanced driver wages, and provided experienced leadership.
These measures resulted in significant cost savings, reduced wait times, improved safety conditions, and eliminated driver turnover. The successful partnership between Lazer and the customer resolved issues and added substantial value to the center’s operations.
CONTACT US